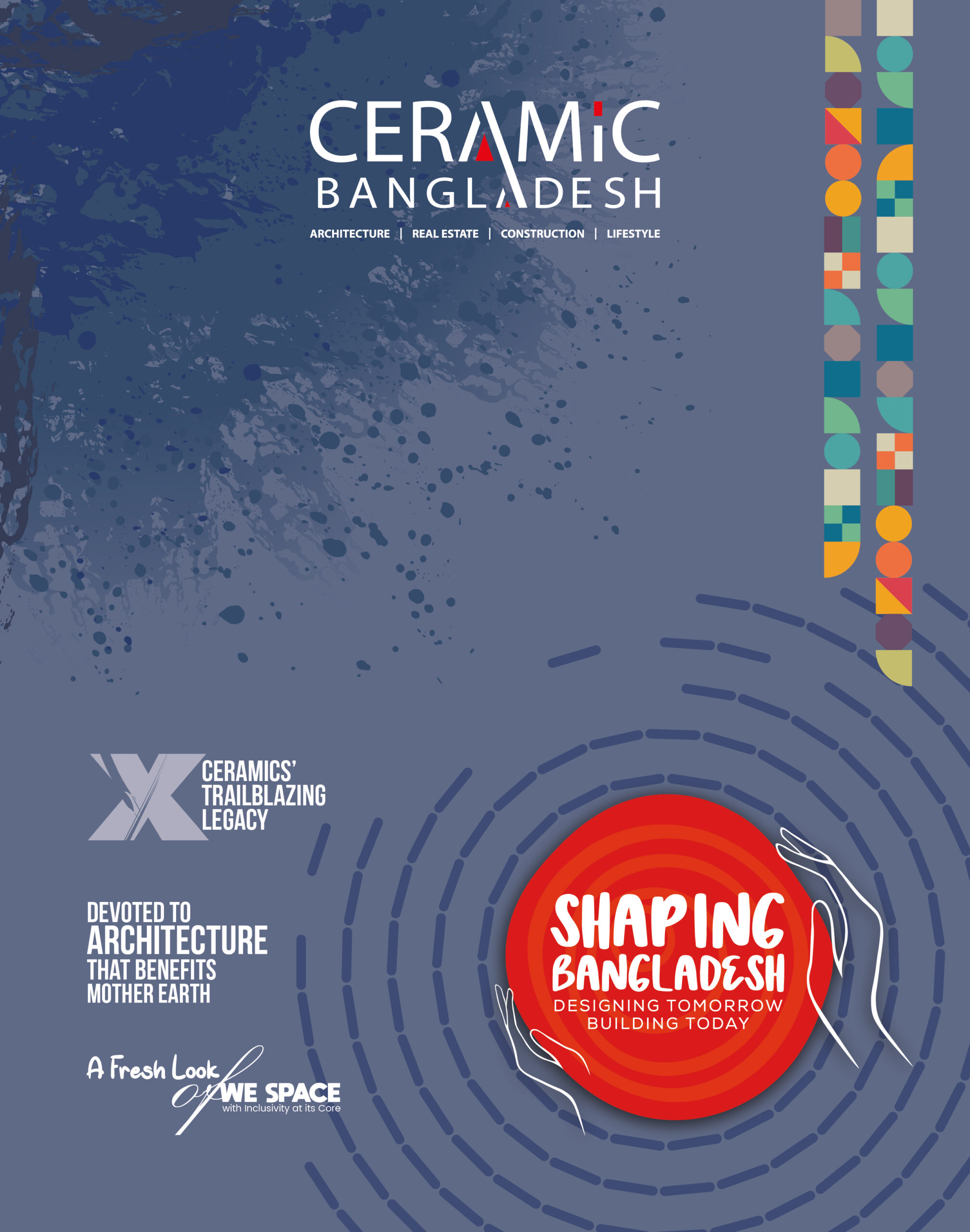
We are all familiar with the Dhaka University and its grandeur. Even now, when major infrastructures shroud the beautiful campus, its thousands of students still enjoy a little retreat among greeneries in, for example, Muktamancha or Suhrawardi Udyan. The same can also be said for all public universities. It’s on one such campus where BUET alum Khandaker Ashifuzzaman Rajon, Principal Architect of Cubeinside Design Limited, studied architecture. Of course, Rajon’s idea of a campus vastly differs from that of private university students. Thus, when tasked with designing a campus for Southeast University (SEU) well within the hustle-bustle of Dhaka, Rajon had to tumble down all his cards and think of fresh ways to give the students of Southeast University some taste of his own campus-going experience. The project being the permanent campus came with the additional worry of how to design the structure that would inspire students to enrol just looking at the place years, even decades, after its novelty factor has worn off. But before we go further into Rajon’s and the Southeast University permanent campus story, allow us to tell you what it is about all private universities competing to move to their permanent campuses. Competition here is particularly good, as all private universities want a permanent campus that is the most student-friendly while being attractive. UGC, the University Grants Commission, recently stipulated that all private universities, without fail and exception, move to a permanent campus that facilitates students with open space, interactive classrooms, and all the amenities that university students abroad enjoy from a campus. So, that triggered the mass relocation of private universities to actual campuses in place of stuffy buildings. Rajon opened his story with the mandatory 50% open space policy in the rulebook for building a new permanent campus. “The idea of a cubic volume in the centre of the campus came from this rule. I wanted the rest of the structure to look over the open space as the centerpiece of the campus. As a by-product, a central courtyard would help dissipate light and aerate its surroundings, like the classrooms, for example. However, the Board wasn’t initially unanimous about the central open space idea, but it was up on completion that they saw my vision behind this design choice, and this later became everyone’s favorite part of the entire campus,” began the architect. But beyond the Board’s stamp of approval, the campus just had to be completed and made fully functional within a very limited window of time, set by the UGC. If you happen to be a current student of SEU or have even visited the place, you may have taken a moment’s pause and thought of how it was even possible to erect an edifice as such in such a constricted amount of time. This is where the seasoned, but young, architect’s ingenuity just begins. If my memory serves well, I remember seeing in the popular cartoon show “Popeye: The Sailor Man” Popeye stacking floors upon floors of a skyscraper with steel I-beams, all in one shift, of course with the help of his special formula spinach, but steel I-beams were the actual hero that allowed for construction at such mind-boggling speeds. I am not inferring that Rajon got his hands on Popeye’s spinach, but being the well-bred architect that he is, he knew that I-beams would be an ideal instrument in his race against time. He explained how: “All the brick and concrete facades of the entire complex give it the impression of an RCC (reinforced cement concrete) structure, but its basic skeleton is made of I-beams. This bought me time! I-beams, like Lego, just have to be joined together using nuts and bolts without trading modern looks for time or structural integrity, but we did trade off some extra money to be able to complete construction in time.” The mission he had in mind to let light dance around the entire complex with the help of a central open space was a massive success. As the structure was shaping up rather quickly, it was instantly visible that the same campus took on different faces because of the changing sunlight that entered at different angles at different hours of the day. As a creator, the play of light and shadow had Rajon all emotional when he laid eyes upon the outcome. “The place would change its look at the change of each season too,” he said. “A few of my acquaintances who study at SEU find the campus quite photogenic. As climates change, they post photos and reels of different parts of the campus on their social media, and from there, I get to observe, from an onlooker’s perspective, how the most important beneficiaries of the campus—who are the students—are lovingly accepting it and are also low-key boasting it on their socials.” All this is to say that a structure made exclusively out of complex mathematics and engineering can also evoke emotions when made with the human angle in the mix. Ever since the permanent campus opened its doors to students in early 2023, the entire place teems with students in any direction imaginable. Not only is that the proper utilisation of space, but it also points towards the inevitable fact that students love their new campus. Everyone is doing what a student does: going in and out of class, singing, laughing, teasing, playing with classmates between classes, and most importantly, enjoying their newfound freedom in such a capacious facility that can house over 12,000 students at once! The former campus building is in the backyard of the new campus. It will be demolished soon and replaced by a new building to house the School of Engineering. It is to be designed by Cubeinside Design Limited as well. “But looking at the design of the new building and the one we just completed, no one will be able to say that the same architecture firm was behind the drawing board of the second one; it’s that different from the
The First Dhaka Elevated Expressway (FDEE) is called a ‘new milestone’ in communications and the project is being implemented under Public-Private Partnership (PPP) arrangement to alleviate traffic congestion in and around the capital. It has already been visible after inauguration of a portion of total of 46.73-kilometre-length with ramps, including a main elevated section spanning 19.73 km in the city. Prime Minister Sheikh Hasina inaugurated the 11.5 km part of it between Hazrat Shahjalal International Airport and Farmgate section, on September 2 with the key objective to shorten the lead time for exports and imports activities. Now people can travel the Airport-Farmgate site in 10 minutes thanks to the FDEE inauguration in the densely populated city. It often takes two hours to travel the 11.5 km due to severe traffic congestion. According to the First Dhaka Elevated Expressway Company Ltd, the total of 46.73-km-long elevated expressway is covering Airport, Kawla, Kuril, Banani, Mohakhali, Tejgaon, Magbazar, Kamalapur, Sayedabad, Jatrabari to Kutubkhali on the Dhaka-Chattogram highway. The entire expressway is expected to be opened for vehicles from Tejgaon to KutubKhali in June 2024. The FDEE project involves construction of a four-lane main carriageway and one elevated link road, comprising: four-lane dual main carriageway of a total length of 19.73 kilometers. It has a four-lane dual link-road carriageway of a total length of 3.1 kilometers. 32 on-off ramps including 16 on-ramps and 16 off-ramps (one-lane carriageway of 5.5 meter width) of a total length of 23.9 kilometers with 8 toll plazas and 43 toll collection booths. Besides the main four-lane dual carriageway and two suspended termini at its ends, it has five interchanges, two elevated links. The approximate total length of the main carriageway Expressway is about 46.73 km including 19.73 km main flyover and 31 km ramps and elevated links. Dhaka-Ashulia, Dhaka-Narayanganj and Dhaka-Chittagong expressways will also be connected with this elevated expressway in future. The project is one of the largest infrastructure projects taken up by the incumbent government spending a total of Tk 13,858 crore to ease traffic congestion. Of them, the cost of Airport-Farmgate section was Tk 8,940 crore. However, the FDEE project is being implemented under the PPP process between the government of Bangladesh, represented by the Bangladesh Bridge Authority (BBA), and the Italian-Thai Development Company Limited (ITD Group), represented by the First Dhaka Elevated Expressway (FDEE) Co. Ltd. According to the authority, around 80,000 vehicles can run on the FDEE a day. Chinese firm China Shandong International Economic and Technical Corporation, one of the three private partners of the PPP project, will operate the control centre. The FDEE is offlimits to three-wheelers and motorcycles. Other vehicles run on the structure at a maximum speed of 60km per hour in expressway and 40km per hour in ramps at the beginning. BRTC bus services commenced on the Expressway. The non-stop service, which began initially, runs with eight double-decker buses from Farmgate to the Airport. Road Transport and Highways authority said cars, SUVs, microbuses with fewer than 16 seats, and trucks with a capacity of less than three tonnes will pay Tk 80 for using the expressway. Trucks with six wheels will pay Tk 320, those with more than six wheels Tk 400, and buses with 16 or more seats Tk 160. Payment is being processed through e-ticketing. Local construction industries are thriving At least 10 local companies are making and supplying materials, such as cement, steel, stone and paint, for constructing the country’s first elevated expressway. Local products in place of imported alternatives are also being used in this mega project. This is not only saving foreign currency but also building the capacity of the local companies. A major portion of the Tk 8,940 crore project is being constructed using local materials. Of the 10 local contributors, six are cement companies while two are steel makers and the others make paint and PVC products. The cement makers are: Shah Cement, Crown Cement, Bashundhara Industrial Complex, Heidelberg Cement, Seven Rings Cement and Premier Cement. The BSRM and GPH Ispat are providing steel for the project while two concerns of RFL Group — RFL Pipe and Fittings, and Rainbow Paints — are supplying necessary pipes and road marking materials. RN Paul, managing director of RFL Group, said they are providing waste and rainwater pipes and fittings for the drainage system of the elevated expressway as well as road marking materials. Mr Paul explained that if local companies do not provide the required construction materials, then they would have to be imported at the cost of huge sums of foreign currency. “So, local companies benefited and also the process helped save foreign currency through such cooperation,” he said. Till September 2023, a total of 66,000 tonnes of steel has been used in the elevated expressway project, with BSRM contributing a majority 52,000 tonnes (80%). Tapan Sengupta, deputy managing director of BSRM, acknowledged that involvement in this type of large project helps local construction material companies grow their capacity and achieve global standards. Sheikh Masadul Alam Masud, founder chairman of the Bangladesh Steel Manufacturers Association, said the local steelmaking capacity has nearly doubled to about 9 million tonnes over the past decade. Local cement manufacturers have increased their production capacity to 6 million tonnes per annum while it was 2 million tonnes annually just 10 years ago. Back to history In January 2011, the certificate authority (CA) was signed between Bangladesh government, represented by Bridges Division, the Ministry of Road Transport and Bridges, acted through Bangladesh Bridge Authority (together the “grantor”), and First Dhaka Elevated Expressway (FDEE) company limited (the “concessionaire”). The ITD, the largest construction company in Thailand, established first Dhaka Elevated Expressway Company Limited (“FDEE”) as a 100%-owned special purpose vehicle, registered in Bangladesh, to accede ITD as the concessionaire in the concession agreement for implementation of the project. The BBA signed deal with Italian-Thai Development Public Company to build the FDEE at a cost of Tk 8,703 crore in January 2011. The agreement was revised and inked again in
Time is NOW for eco-friendly clay-made roofing tiles and now is TIME for tile makers. They are the Bangladeshi makers of clay tiles who have gone global as their tiles have opened up the door of a huge export possibility, especially to Europe. The making of clay tiles is simple but it needs amazing artistry as well as artisanal skills. Fluffy mud is made by mixing soil and water. It then dries in the sun and is burned only to turn into clay gold. The artistic tiles with Bengal clay have revolutionised the style. However, clay artisans were once about to lose their hopes and dreams with their centuries of tradition. They then have turned the corner and things are looking up with the coming of the modern machine-driven industry. The clay artisans have turned around to weave a new web of hopes and dreams. Famed for its ‘Tiles Empire’ over the years, Satkhira has eco-friendly roofing tiles to its credit. Kolaroa Bazar in Kolaroa upazila, some 18 kilometres of district headquarters, is one of the prosperous trading points in Satkhira. Murarikathi village is located just 1.0 km away from the upazila headquarters along the border of the district. The artisans of Murarikati-Sripatipur have built an empire of various sorts of roofing tiles. The village, also called Kumarpara, has now got the moniker ‘Italy Town’ plausibly for exporting a massive volume of tiles to the European country. Tile factories used to produce 700-800 containers a year just a few years back. Some 300-400 container tiles were exported to Italy through Mongla seaport. The price of the product per container is average US$ 15000 Eco-friendly tiles Eco-friendly tiles There is a huge local market for roofing tiles if these hand-made tiles are given a more modern touch and the initiative is taken to use them as an artisanal tile in buildings and structures. During the British raj, cottages, offices or residences of the gentlemen used to have tiles at the peak that are still visible in the ancient architecture of Britain. Although a large number of potters have left Bangladesh, some in Kolaroa have kept the traditional tile industry alive in the frontier district. Until the mid-1960s, there were hardly any houses in the country that did not have a tile-made house or two. As it came cheap, roofing tiles became popular after rice and wheat straw-built structures. The structures were felt cool and comfortable during the summer. How Palparaenters European market The traditional tiles industry almost sank into atrophy when the potters associated with tile production left the country in the mid-60s. Satish Chandra Pal, a native of Palpara in Kolaroa, started crafting house canopy tiles in about 1952. From there, potters spread across the country. As Mr Satish Chandra died after independence, the pottery business simply collapsed. Due to their deep-rooted poverty, many artisans left their ancestral profession. With the passage of time, the potters have changed. They are now making tiles using clay. In 2003, local potters created a revolution by pouring clay into a wooden frame and drying it in the sun, making Bengali tiles in line with Italian design. Since then, Bengali tiles are being exported to Italy How are the legacy-bearers? Among those artisans is Gostho Chandra Paul, the president of Kolaroa Upazila Tali Malik Samity [Tiles Owners Association] and also proprietor of Kolaroa Clay Tiles. But he now struggles to survive as his long-cherished art is on the verge of extinction for a number of reasons. The 60-year-old Paul, who has a three-member family, is producing 1,000 units of tiles at his factory per diem. Each unit is currently being sold at Tk 8.0. He earns Tk 1.6-1.7 million per annum. Getting disgruntled and disappointed over the waning business situation, most owners and workers associated with this industry have already lost their jobs. Mr Paul observed that modernity has affected almost all sectors of the country. However, the tiles industry is yet to get the touch of modernity. Production costs have increased manifold, but the price of tiles has not increased. Mr Paul’s forefathers launched crafting eco-friendly roofing tiles in 1947. However, it all started for Mr Paul in 1986 when he set himself up in business with Tk 3,000 only. Ten workers were employed at his factory when he started crafting eco-friendly roofing tiles traditionally. His uncle told him to be self-reliant and build his own future through the long traditional business, which he acquired lineally. But at least 40 tile factories got shut down in the past six years due to their persistent business losses. Now, the number of factories there is about 12. Almost 6,000 workers become unemployed and only 600 are absorbed elsewhere. For generations, the Pal community in the locality has been contributing a lot to this thriving sector. Mr Paul is also committed to continuing their forefathers’ business at any. In 2003, this clay tile was first exported to Italy. Businessman Ruhul Amin exported the eco-friendly tiles there. Arno Export Import, Shuvo Trade Limited, FH Khan Limited, Maa Cottos Inc., Nikita International, Koto Innovator, JK International, Polo Epo Organic Tiles and D Chandra Paul have followed Mr Amin’s footsteps. They are exporting tiles to Italy, Dubai, France, the UK, Australia, Germany and the Netherlands. Mr Chandra Paul, proprietor of Kolaroa Clay Tiles, said Mr Amin continued to look for suitable soil in different parts of the country for exporting tiles to Italy. Finally, Mr Amin found his desired soil in Murarikati area. He is the pioneer in exportable tile business. As the number of roofing tile factories increased in Kolaroa until 2019, the stock remained high at the time. Every year, 300-400 containers of tiles went to Italy. Such tiles are manufactured and sold for 6-7 months in a year. Usually, tile-making season starts from October and continues until the May-June period. Tiles cannot be crafted during the rainy season. Foreigners are using the tiles for floors and walls of their houses because of its eco-friendly nature.
Popular Post