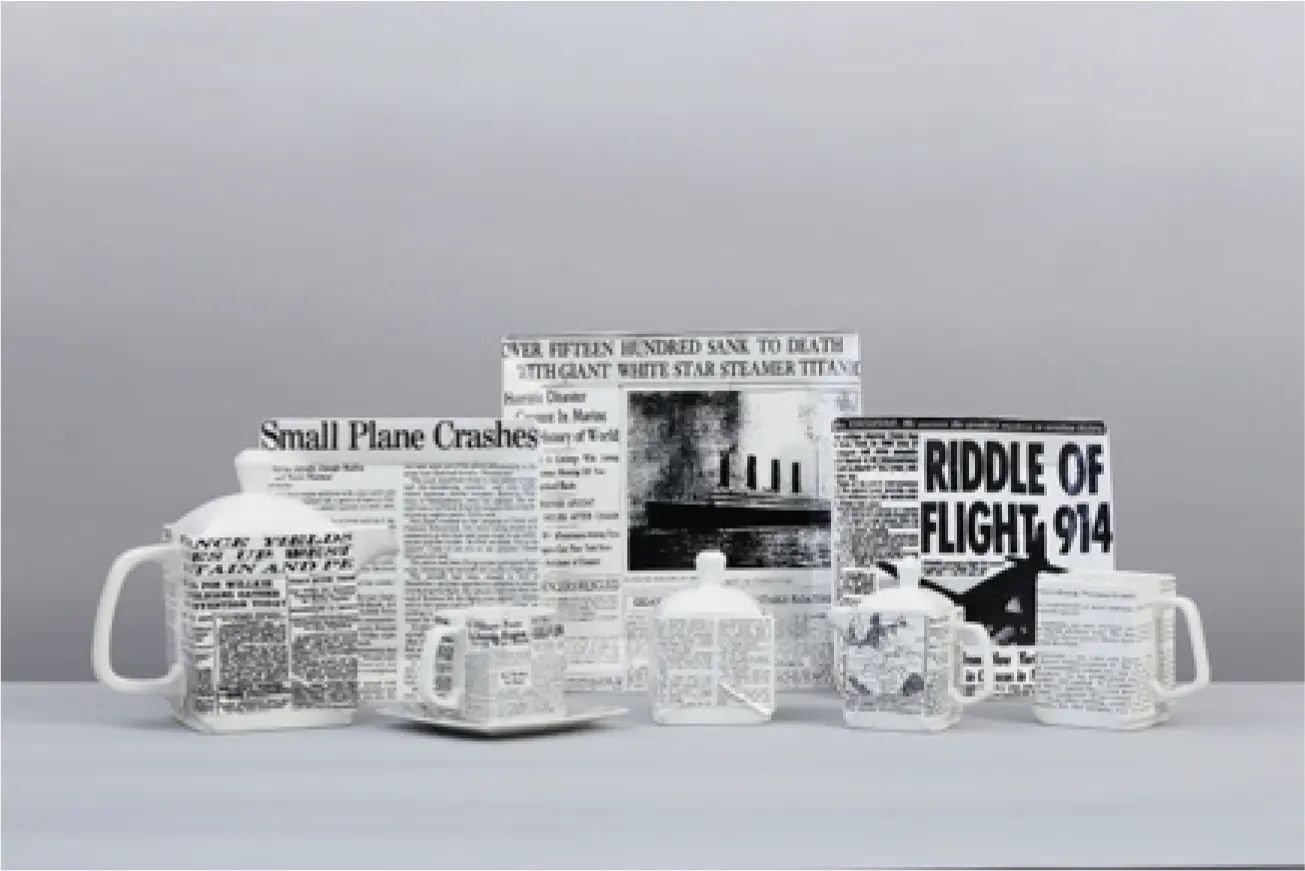
For ceramics, you only get one chance to impress a viewer. The first impression, which is notoriously, the last, has to be a solid ¨I like the design¨ or else no matter how the shape or the glazing is, the same person will not give a second look at it. This is where designers come in. The designer envisions shapes and colours and creates enthralling pieces of ceramic ware. S/he not only comes up with the idea of the product, but also decides on the technical aspects that work behind every output. The process, the casting, is formed, the machines are heated up, the raw material has to be loaded, and at one stage, the whole thing goes through 1350 degree Fahrenheit temperature where it’s turned into a soft liquid like structure. The product is then balanced with the gravitational pull so that it stands upright. Then there is glazing, firing, later aspects of forming and so on.
After a bunch of hurdles, we come up with that one glass or vase you bought from a store and is now holding freshly bought flowers in the corner of your living room. In search of more depth into the life of a ceramic designer, the Ceramic Bangladesh author visited Mr. Rudro Badal, General Manager of Paragon Ceramic Industries Ltd. During the conversation, he discussed his early years as a designer, his blooming interest in ceramics and clay art and the rest of the journey.
In 1983, Rudro Badal was a student of drawing, painting, and sculpture dept. at Charukola Institute (Art Institute), Dhaka and had knowledge of basic design at the time. He enjoyed poetry and designing, and worked with wood and clay. Entering into the ceramic industry, he realised that most designers didn’t have basic education. So working with them at the time was difficult. However, to design his pieces and experiment multiculturally, he needed a little bit of support.
Mr. Rudro mainly started with ceramic modeling and is a designer. At the time of his entry into the industry as a professional, companies would replicate or go with conventional designs rather than using a designer to create something new. There wasn’t a go-ahead from their higher officials, so designers would have no room to express their creativity. ¨Everyone was stuck in the old ways,¨ as Mr Rudro said from his experience. This is back in 1992.
Hoping to find a better platform to express himself, Mr. Rudro joined Bengal Fine Ceramics Ltd in 1992. But unfortunately the scene there was the same. The company would make replicas or an old shaped model rather than design themselves. The local and international market was inclined towards European designs, but Mr. Rudro had other design ideas in mind.
In 1998, Monno Ceramics management thought progressively and inspired Mr. Rudro and his team to create the kind of artwork they wanted to create. Farr Ceramics Ltd was one of the prominent ones, which at the time wanted their help as well to create designs from scratch. Things started to look up for designers, and Mr Rudro has been training the newcomers ever since. Looking back, almost every designer in the industry has been trained by the hands of Mr Rudro. And these students are a bunch of talented folks with the drive to create something new.
Mr. Rudro designed a huge collection of Arong’s displays. His current company supplies to the leading brand. ¨We would fix technical errors in designs in products we bring in. for new ideas, we had difficulties marketing our designs at first, but soon the brand Porcelaina came out and showcased all our work. It is doing really well. Most of my designs have an influence from African Pottery. I even call them my Amazon shapes,¨ Mr Rudro said.
Rudroś Hobby
“Ï enjoy reading and writing. From a very young age I contributed to newspapers and magazines and I still do it out of love for arts and literature. One such publication I wrote for was Jai Jai Din.¨ Tips for newcomers in the industry ¨You can have technical knowledge but that won’t take you far. You need to have a deep understanding of culture and how it influences ceramics. And you need passion as well.¨ Mr. Rudro also mentioned that learning to understand moisture is a hack that most newcomers should learn first. Of the most recent crisis in the industry The biggest crisis at the time is gas. “We are facing difficulty with availability of gas, so we use CNG (compressed natural gas) as backup. After a lot of internal discussions, we decided that we might use coal gas to produce ceramic wares in future. Maybe coal gas will give us spotted or darker products but those can be turned into fashion as well.