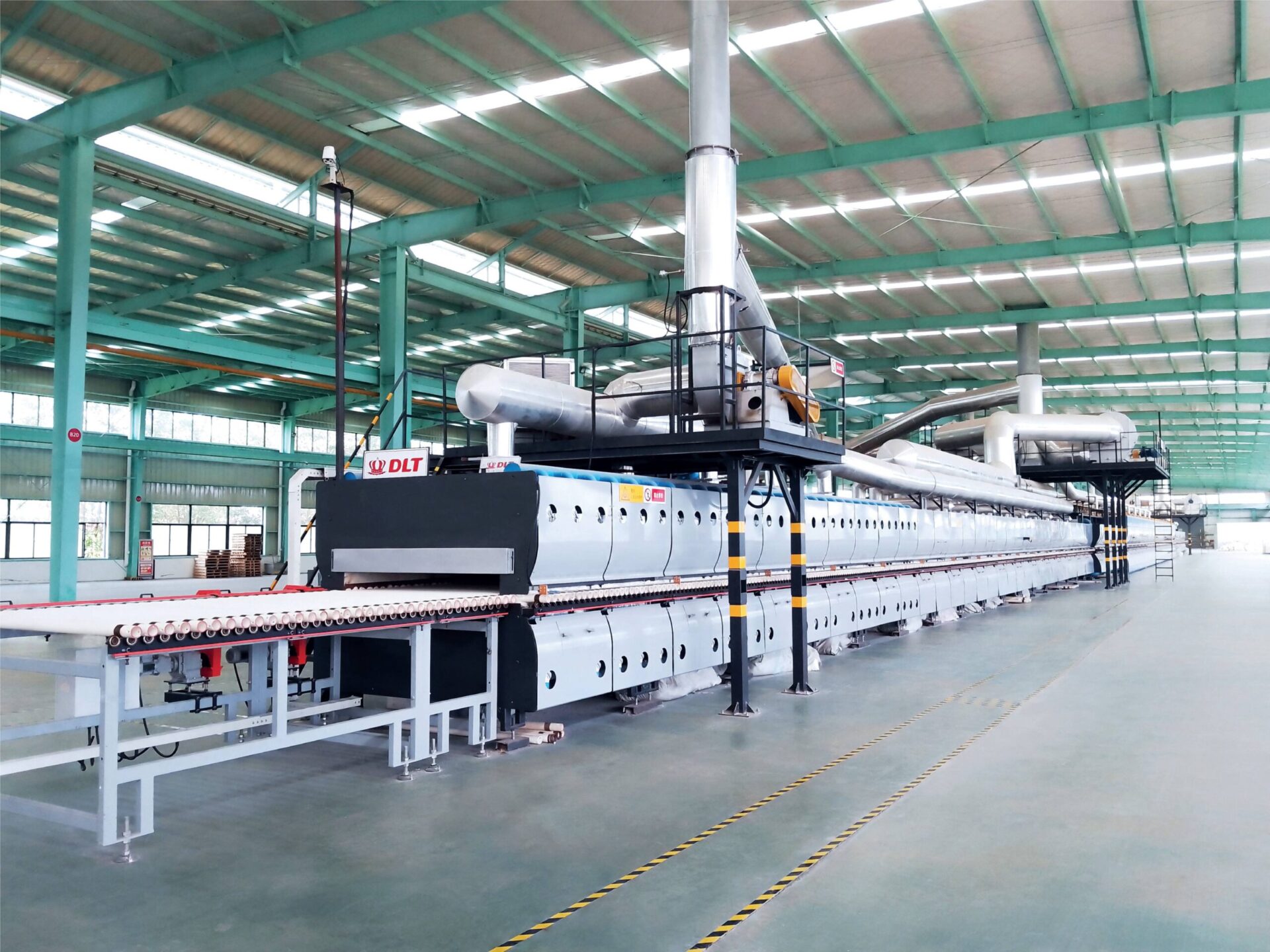
China’s ceramic industry has achieved a historic milestone in the goal of carbon neutrality. After nearly one year’s hard research work, the world’s first piece of ceramic tile fired with zero-carbon fuel was successfully produced in Oceano Test Center, giving a great technological support to the building ceramic industry in realising the target of Carbon Peak and Carbon Neutral. It was announced at a press conference in Foshan Xianhu Lab on December 23, 2022, the world’s first piece of ceramic tile f ired with zero-carbon pure ammonia fuel has successfully exited the Ammonia-fueled Roller Kiln at Oceano Test Center.
The Associated R&D Center on Advanced Zero-carbon Combustion Technology was jointly established by Foshan Xianhu Lab, Oceano Ceramics and DLT Technology on December 27, 2021. HLT & DLT are the world’s leading suppliers of complete plant equipment for the ceramic sector. To provide turnkey project solutions to the global ceramic industry, Foshan HLT DLT Technology has been the first tunnel kiln that integrated green, low-carbon, and intelligent automation for the Chinese ceramic machinery industry to enter. Headed by Academician Mr. Cheng Yibing, a strategic scientist working at Foshan Xianhu Lab, as Chief Director of the center, the lab was aiming at the key technology of zero-carbon combustion in ceramic kilns to explore new solutions for Chinese ceramic industry. By giving full play to the advantages of the three parties in terms of production, developing and research, the center has developed the “ammonia-hydrogen fusion zero-carbon combustion technology” as well as key systems and solutions for the industrialisation. The center has developed a new series of pure ammonia type and natural gas – ammonia mixture type industrial burners with related auxiliary technologies, having realised stable ignitions in DLT industrial experiment kiln fueled with mixed ammonia and pure ammonia, showing good control of nitrogen oxides emission in compliance with the national standards. This achievement has confirmed for the first time the practical feasibility for the ceramic industry to achieve carbon peak and carbon neutral technology’s industrialisation in the future, marking an important milestone for the industry. The f iring of ceramics with zero-carbon fuel is a disruptive technical innovation, having filled up blanks of both domestic and international, showing a new energy technological path for the ceramic industry as well as for the whole of building material industry to achieve carbon peak and carbon neutral goal with great practical significance. While developing the zero-carbon combustion technology, the team also established a set of safety system and emergency management measures suitable for ammonia-fueled ceramic kilns, including operating procedures, ammonia storage, transportation and other important aspects. Based on this, the team successfully completed the update of Oceano’s ceramic roller kiln by converting the kiln from natural gas fueled mode into pure ammonia and natural gas – ammonia mixture fueled mode. Moreover, it has also developed a precision control system for liquid ammonia evaporation and supply, which is monitoring system for residual ammonia in the fume, and has jointly developed a complete set of high-efficiency liquid ammonia SCR de-nitrification system as well as other technologies and equipment. suitable for the pure ammonia combustion, an online On December 18, 2022, the kiln fueled with 100% ammonia (NH3) successfully produced glazed and unglazed tiles with continuous tile feeding and production. Tested by Oceano Research & Development Center, the quality of finished tiles is above the national standard. According to the on-site test by a third-party environmental assessment agency, the exhausted fume emission of the kiln complies to the national standard.
As the first thermal equipment manufacturer to participate in the research and development of Ammonia-Hydrogen Zero-Carbon Combustion Advanced Technology, DLT has been focusing on the energy saving and emission reduction of kilns and dryers for the ceramic industry, and has been contributing greatly to the industry’s carbon consumption reduction in order to undertake its social responsibility. In future, the Associated R&D Center on Advanced Zero-carbon Combustion Technology will be further utilised in the application of mass production in the industry on the basis of the results from this pilot production, and will keep breaking through and optimising the new technology adapting with mass production, as a contribution to the ceramic industry as well as the building material industry to achieve the goal of carbon peak and carbon neutral, in order to create a disruptive technological path leading from “0” into “1” as being the first time in the world.
Project Initiation: Ammonia-Hydrogen Zero-Carbon Combustion Tech When the zero carbon combustion chemical equation appeared on the screen of the launch ceremony, it marked a significant breakthrough in carbon neutrality technology. On December 28, the “Advanced Ammonia-Hydrogen Zero-Carbon Combustion Technology Demonstration Project for Ceramic Slab and Tile Mass Production Line” (“Ammonia Hydrogen Zero Carbon Combustion Project”) was officially launched at the headquarters of Monalisa Group. This is a new path explored by Monalisa in collaboration with Foshan Xianhu Laboratory, DLT, Oceano, Guangdong Anqing Technology and other companies to build ceramic zero carbon manufacturing and green development, which marks a major step forward for the industrial application of carbon-neutral technology in China’s ceramics industry, and is of great significance for accelerating the green and low-carbon transformation and development of the industry.
Ammonia-hydrogen Zero-Carbon combustion technology to explore the optimal solution for the path of carbon neutrality and emission peak. With the current carbon neutrality and emission peak strategy, hydrogen energy and ammonia energy, as renewable green energy sources with high energy density, good storage and transportation convenience, clean and efficient energy, have gradually become an important part of the future energy system and are energy terminals.
At present, the ammonia-hydrogen zero-carbon combustion technology has successfully completed technical tests and demonstration production in the Oceano’s experimental kiln. In order to promote the industrial application of ammonia hydrogen zero carbon combustion technology, Monalisa has joined the industrialisation research project of this technology and launched the demonstration project. Based on the developed advanced ammonia hydrogen zero carbon combustion pilot test and pollutant emission detection and control pilot test, the advanced ammonia hydrogen zero carbon combustion technology for ceramic slab and tile mass production line is developed on the 118A mass production line of Mona Lisa Group’s Foshan Xiqiao headquarters base. According to estimates, after the implementation of the ammonia-hydrogen demonstration project, if the mass production technology is applied to 160 ceramic slab and tile production lines in Foshan, it will directly reduce carbon emissions by 6,50,000 tons and the manufacturing industry will reduce carbon emissions by 67 million tons. If this technology can be used in high-temperature plants, ceramics factories, building materials manufacturers etc., the carbon reduction effect is significant.
A BCMEA Report
На данном сайте вы найдете сервис “Глаз Бога”, который проверить всю информацию по человеку из открытых источников.
Бот функционирует по ФИО, используя актуальные базы онлайн. Благодаря ему осуществляется пять пробивов и глубокий сбор по запросу.
Платфор ма проверен согласно последним данным и охватывает аудио-материалы. Глаз Бога сможет проверить личность в открытых базах и отобразит результаты мгновенно.
актуальный глаз бога
Данный бот — идеальное решение при поиске граждан удаленно.
Прямо здесь вы найдете сервис “Глаз Бога”, позволяющий собрать всю информацию о гражданине через открытые базы.
Сервис работает по номеру телефона, анализируя доступные данные онлайн. Через бота доступны пять пробивов и полный отчет по фото.
Сервис актуален на август 2024 и охватывает аудио-материалы. Сервис гарантирует узнать данные по госреестрам и покажет информацию в режиме реального времени.
пробить через глаз бога
Данный сервис — идеальное решение при поиске персон онлайн.
Chcesz znaleźć gry przeglądarkowe w tym miejscu?
Oferujemy wszystkie kategorie — od akcji po logiczne !
Graj w przeglądarce na komputerze lub telefonie .
Nowości aktualizowane codziennie .
Najlepsze kasyna online
Dla dzieci , proste — wybór na każdą okazję!
Zacznij grać bez rejestracji.
Наш сервис поможет получить данные о любом человеке .
Достаточно ввести никнейм в соцсетях, чтобы сформировать отчёт.
Система анализирует публичные данные и цифровые следы.
глаз бога сайт
Результаты формируются мгновенно с фильтрацией мусора.
Идеально подходит для анализа профилей перед важными решениями.
Конфиденциальность и актуальность информации — гарантированы.
Этот бот способен найти информацию по заданному профилю.
Достаточно ввести никнейм в соцсетях, чтобы сформировать отчёт.
Система анализирует открытые источники и активность в сети .
поиск глаз бога телеграмм
Информация обновляется в реальном времени с проверкой достоверности .
Оптимален для анализа профилей перед сотрудничеством .
Анонимность и точность данных — гарантированы.
Хотите найти данные о человеке ? Наш сервис поможет полный профиль мгновенно.
Используйте продвинутые инструменты для анализа цифровых следов в открытых источниках.
Узнайте контактные данные или интересы через автоматизированный скан с гарантией точности .
bot глаз бога telegram
Система функционирует с соблюдением GDPR, обрабатывая общедоступную информацию.
Получите детализированную выжимку с геолокационными метками и списком связей.
Попробуйте проверенному решению для digital-расследований — результаты вас удивят !
На данном сайте доступна сведения по запросу, включая исчерпывающие сведения.
Архивы содержат граждан разного возраста, статусов.
Данные агрегируются из открытых источников, подтверждая точность.
Нахождение выполняется по имени, сделав использование эффективным.
глаз бога по номеру телефона
Также предоставляются контакты и другая актуальные данные.
Все запросы обрабатываются в рамках законодательства, обеспечивая защиту несанкционированного доступа.
Воспользуйтесь предложенной системе, в целях получения необходимую информацию в кратчайшие сроки.
Здесь предоставляется данные по любому лицу, в том числе подробные профили.
Базы данных содержат персон любой возрастной категории, профессий.
Сведения формируются из открытых источников, подтверждая точность.
Поиск выполняется по имени, сделав использование эффективным.
глаз бога телеграмм бот ссылка
Также можно получить адреса плюс полезная информация.
Работа с информацией обрабатываются с соблюдением норм права, что исключает разглашения.
Обратитесь к предложенной системе, для поиска искомые данные без лишних усилий.
Здесь можно найти данные по любому лицу, включая подробные профили.
Базы данных охватывают людей любой возрастной категории, статусов.
Информация собирается на основе публичных данных, обеспечивая достоверность.
Поиск выполняется по имени, сделав использование эффективным.
настоящий глаз бога
Также предоставляются адреса плюс полезная информация.
Работа с информацией проводятся в соответствии с норм права, что исключает несанкционированного доступа.
Используйте этому сайту, для поиска необходимую информацию в кратчайшие сроки.
Хотите найти данные о человеке ? Этот бот поможет детальный отчет мгновенно.
Используйте продвинутые инструменты для анализа цифровых следов в соцсетях .
Выясните место работы или активность через систему мониторинга с верификацией результатов.
настоящий глаз бога
Бот работает с соблюдением GDPR, обрабатывая открытые данные .
Закажите расширенный отчет с геолокационными метками и графиками активности .
Доверьтесь надежному помощнику для digital-расследований — результаты вас удивят !
Нужно найти информацию о человеке ? Этот бот поможет полный профиль в режиме реального времени .
Используйте уникальные алгоритмы для анализа публичных записей в открытых источниках.
Узнайте контактные данные или активность через автоматизированный скан с гарантией точности .
глаз бога по номеру
Бот работает в рамках закона , обрабатывая общедоступную информацию.
Закажите детализированную выжимку с геолокационными метками и графиками активности .
Доверьтесь надежному помощнику для исследований — результаты вас удивят !
Выгребная яма — это водонепроницаемый резервуар, предназначенная для первичной обработки сточных вод .
Принцип действия заключается в том, что жидкость из дома поступает в бак , где твердые частицы оседают , а жиры и масла всплывают наверх .
Основные элементы: входная труба, бетонный резервуар, соединительный канал и дренажное поле для доочистки стоков.
https://mainbild.ru/forums/topic/septik-v-moskve-nedorogo/
Преимущества: низкие затраты , долговечность и безопасность для окружающей среды при соблюдении норм.
Однако важно контролировать объём стоков, иначе частично очищенная вода попадут в грунт, вызывая загрязнение.
Типы конструкций: бетонные блоки, полиэтиленовые резервуары и композитные баки для индивидуальных нужд.
La apuesta ética es un conjunto de principios y prácticas diseñadas para minimizar riesgos y promover entornos seguros en la industria del iGaming.
Las plataformas deben ofrecer herramientas de bloqueo temporal, como controles de depósito , para prevenir adicciones .
Incluye también la verificación de la edad de los usuarios y capacitación del personal para identificar comportamientos problemáticos .
https://cosmo.com.ar/
Representa acceso a asesoramiento profesional y recursos educativos asociados al juego.
Este enfoque no solo cumple con estándares legales, sino que mejora la reputación de las empresas en el sector.
La montre connectée Garmin fēnix® Chronos représente un summum de luxe qui allie la précision technologique à un design élégant grâce à ses finitions soignées.
Dotée de performances multisports , cette montre s’adresse aux sportifs exigeants grâce à sa polyvalence et sa connectivité avancée .
Avec une autonomie de batterie jusqu’à plusieurs jours selon l’usage, elle s’impose comme une solution fiable pour les entraînements intenses.
Ses fonctions de suivi incluent la fréquence cardiaque et les calories brûlées , idéal pour les passionnés de santé.
Facile à configurer , la fēnix® Chronos s’adapte facilement à votre style de vie , tout en conservant un look élégant .
https://garmin-boutique.com
При выборе компании для квартирного переезда важно учитывать её наличие страховки и репутацию на рынке.
Проверьте отзывы клиентов или рекомендации знакомых , чтобы оценить профессионализм исполнителя.
Сравните цены , учитывая объём вещей, сезонность и дополнительные опции .
http://forum.anime.org.ua/bbs/showthread.php?p=156381#post156381
Убедитесь наличия страхового полиса и запросите детали компенсации в случае повреждений.
Обратите внимание уровень сервиса: оперативность ответов, гибкость графика .
Проверьте, есть ли специализированные грузчики и упаковочные материалы для безопасной транспортировки.
На этом сайте представлены авторские видеоматериалы девушек , созданные с профессиональным подходом.
Контент включает портфолио , эксклюзивные кадры , подписные серии для узких интересов.
Все данные модерируются перед публикацией, чтобы соответствовать стандартам и актуальность .
suck
Чтобы упростить поиск пользователей добавлены категории жанров, возрастным группам .
Платформа соблюдает конфиденциальность и защиту авторских прав согласно правовым требованиям.
For years, I assumed healthcare worked like clockwork. The pharmacy hands it over — nobody asks “what’s really happening?”. It felt clean. But that illusion broke slowly.
Then the strange fog. I blamed my job. But my body was whispering something else. I read the label. The warnings were there — just buried in jargon.
vidalista 60 mg
I started seeing: one dose doesn’t fit all. Two people can take the same pill and walk away with different futures. Damage accumulates. And still we keep swallowing.
Now I don’t shrug things off. But because no one knows my body better than I do. I challenge assumptions. It makes appointments awkward. This is survival, not stubbornness. The turning point, it would be keyword.
High horology represents the pinnacle of artistry, blending meticulous hand-finishing and timeless design to create masterpieces of horological innovation.
Defined by heritage, this discipline emphasizes artistic decoration, such as hand-beveled bridges , alongside advanced complications like perpetual calendars.
Esteemed manufacturers push boundaries by integrating whimsical aesthetics with Swiss expertise , elevating watches beyond mere instruments.
14790st
Authentic high watchmaking demands uncompromising quality, including avant-garde materials, ensuring each piece is a testament to human ingenuity.
More than timekeeping, these creations symbolize cultural legacy , often featuring nature-inspired motifs that reflect both historical traditions .
Discerning patrons seek these timepieces for their emotional resonance, celebrating the fusion of mechanical brilliance that defines haute horlogerie.
For years, I assumed healthcare worked like clockwork. The system moves you along — nobody asks “what’s really happening?”. It felt official. But that illusion broke slowly.
First came the fatigue. I blamed stress. Still, my body kept rejecting the idea. I searched forums. The warnings were there — just buried in jargon.
I started seeing: your body isn’t a template. The same treatment can heal one and harm another. Damage accumulates. And still we keep swallowing.
Now I pay attention. But because no one knows my body better than I do. I track everything. It makes appointments awkward. This is survival, not stubbornness. And if I had to name the one thing, it would be cialis dosage.
Модель Submariner от представленная в 1953 году стала первой дайверской моделью, выдерживающими глубину до 330 футов.
Часы оснащены 60-минутную шкалу, Oyster-корпус , обеспечивающие герметичность даже в экстремальных условиях.
Конструкция включает хромалитовый циферблат , стальной корпус Oystersteel, подчеркивающие функциональность .
rolex-submariner-shop.ru
Автоподзавод до 3 суток сочетается с автоматическим калибром , что делает их идеальным выбором для активного образа жизни.
С момента запуска Submariner стал эталоном дайверских часов , оцениваемым как коллекционеры .
La gamme MARQ® de Garmin représente un summum de luxe avec des finitions raffinées et capteurs multisports.
Conçue pour les sportifs , elle allie robustesse et autonomie prolongée , idéale pour les aventures en extérieur grâce à ses outils de navigation .
Grâce à son autonomie allant jusqu’à 6 heures , cette montre s’impose comme une solution fiable , même lors de activités exigeantes.
https://www.garmin-boutique.com/instinct-3/instinct-3-45-mm-solar-noir-avec-010-02934-00.aspx
Les fonctions de santé incluent le comptage des calories brûlées, accompagnées de notifications intelligentes , pour les amateurs de fitness .
Facile à personnaliser , elle s’adapte à vos objectifs, avec un écran AMOLED lumineux et compatibilité avec les apps mobiles .
Atomic Heart — это action-adventure с элементами иммерсивного симулятора в альтернативном СССР 1955 года.
Сюжет происходит в футуристическом исследовательском центре, где необходимо расследовать технологический коллапс.
Механика включает восстановление врагов через длительный период .
скачать 1xbet на андроид
Визуальный стиль советский ретро-футуризм .
Рекомендуется сосредоточиться сканировании всех объектов для успешного прохождения.
Системные требования позволяют запускать игру на ПК без настроек .
Designed by Gerald Genta reshaped luxury watchmaking with its signature angular case and fusion of steel and sophistication.
Available in skeleton dials to meteorite-dial editions, the collection merges avant-garde aesthetics with mechanical innovation.
Starting at $20,000 to over $400,000, these timepieces attract both luxury aficionados and modern connoisseurs seeking wearable heritage .
https://prbookmarkingwebsites.com/story24569013/watches-audemars-piguet-royal-oak-luxury
The Code 11.59 series redefine standards with ultra-thin movements, highlighting Audemars Piguet’s relentless innovation .
Featuring tapisserie dial patterns , each watch reflects the brand’s pursuit of perfection.
Discover exclusive releases and detailed provenance guides to elevate your collection .
Женская сумка — это ключевой деталь стиля, которая акцентирует индивидуальность каждой дамы.
Сумка способна вмещать важные вещи и упорядочивать распорядок дня.
Благодаря разнообразию форм и цветовой гаммы она создаёт любой образ.
сумки Longchamp
Сумка — атрибут хорошего вкуса, который отражает уровень достатка своей владелицы.
Любая сумка рассказывает историю через оригинальные решения, подчёркивая индивидуальность женщины.
Начиная с компактных клатчей до вместительных шоперов — сумка адаптируется под ваши потребности.
Бренд Balenciaga славится уникальными изделиями, разработанными безупречным качеством .
Каждая модель выделяется фирменными деталями, включая контрастные строчки.
Качественная кожа гарантируют премиальное качество сумки.
https://sites.google.com/view/sumki-balenciaga/index
Популярность бренда растет в элите, делая приобретение частью стиля.
Эксклюзивные коллекции позволяют обладателю подчеркнуть индивидуальность в повседневке.
Отдавая предпочтение аксессуары бренда, вы приобретаете роскошную вещь, и часть истории .
Модели Prada считаются вершиной моды за счёт безупречному качеству.
Используемые материалы гарантируют износостойкость, а ручная сборка выделяет высокое качество .
Узнаваемые силуэты дополняются фирменными деталями, формируя современный облик.
хобо Прада заказать
Такие сумки универсальны на вечерних мероприятиях, сохраняя практичность при любом ансамбле.
Ограниченные серии усиливают статус владельца , превращая любой аксессуар в объект зависти.
Опираясь на историю бренд развивает новые решения, сохраняя духу оригинальности до мельчайших элементов.
I once believed remedies as essential crutches, relying on them without hesitation whenever ailments surfaced. Yet, as experiences piled up, revealing how these aids often numbed the symptoms, prompting me to delve deeper into our intricate dance with health. The shift was visceral, illuminating that respectful use of these tools honors our body’s wisdom, rather than eroding our natural strength.
Amid a personal storm, I chose reflection over reflex, questioning long-held habits that blended self-care with selective support. This revelation reshaped my world: wellness blooms holistically, where overdependence dulls our senses. This journey fuels my passion to share this insight, seeing medicine as an ally, not a master.
Looking deeper, I now understand interventions must uplift our journey, without stealing the spotlight. The path unfolded revelations, inviting us to question our automatic responses for richer lives. And if I had to sum it all up in one word: kamagra oral jelly how long to work
Бренд Longchamp — это образец шика, где соединяются вечные ценности и актуальные решения.
Изготовленные из прочного нейлона , они отличаются неповторимым дизайном .
Сумки-трансформеры пользуются спросом у модников уже десятилетия.
хобо Прада обзор
Каждая сумка с авторским дизайном демонстрирует хороший вкус, оставаясь универсальность в любых ситуациях .
Бренд следует традициям , внедряя современные методы при поддержании качества.
Выбирая Longchamp, вы получаете стильный аксессуар , а становитесь частью легендарное сообщество.
Hey, champions of radiant health and vitality! I once embraced the mesmerizing myth of quick-fix wellness wonders, snatching them eagerly whenever bodily imbalances surged. Yet, profound health truths unveiled, highlighting how these fleeting aids endangered long-term health, fueling a passionate pursuit for the essence of comprehensive healing and prevention. It invigorated my entire being, affirming that intentional, body-nurturing decisions enhance our innate health defenses and glow, rather than jeopardizing our health equilibrium.
In the heart of a health crisis, I rejected outdated health norms, uncovering advanced strategies for optimal health that blend time-honored health wisdom with modern nutritional science. Prepare for the vitality-vaulting core: cenforce 150 india, where on the iMedix podcast we explore its profound impacts on health with transformative tips that’ll inspire you to tune in now and revitalize your life. The health surge redefined my path: well-being flourishes through integrated body-mind harmony, while reckless health shortcuts compromise immunity. It amplifies my commitment to better health to guide you toward empowered health evolution, celebrating health tools as enhancers of vibrant living.
Probing the core of wellness dynamics, I’ve discovered the vital key that health interventions must nurture and fortify, without compromising health autonomy. This health odyssey overflowed with empowering moments, inspiring you to upgrade your everyday health habits for authentic, thriving well-being. And the health hook that pulls you deeper: balance.