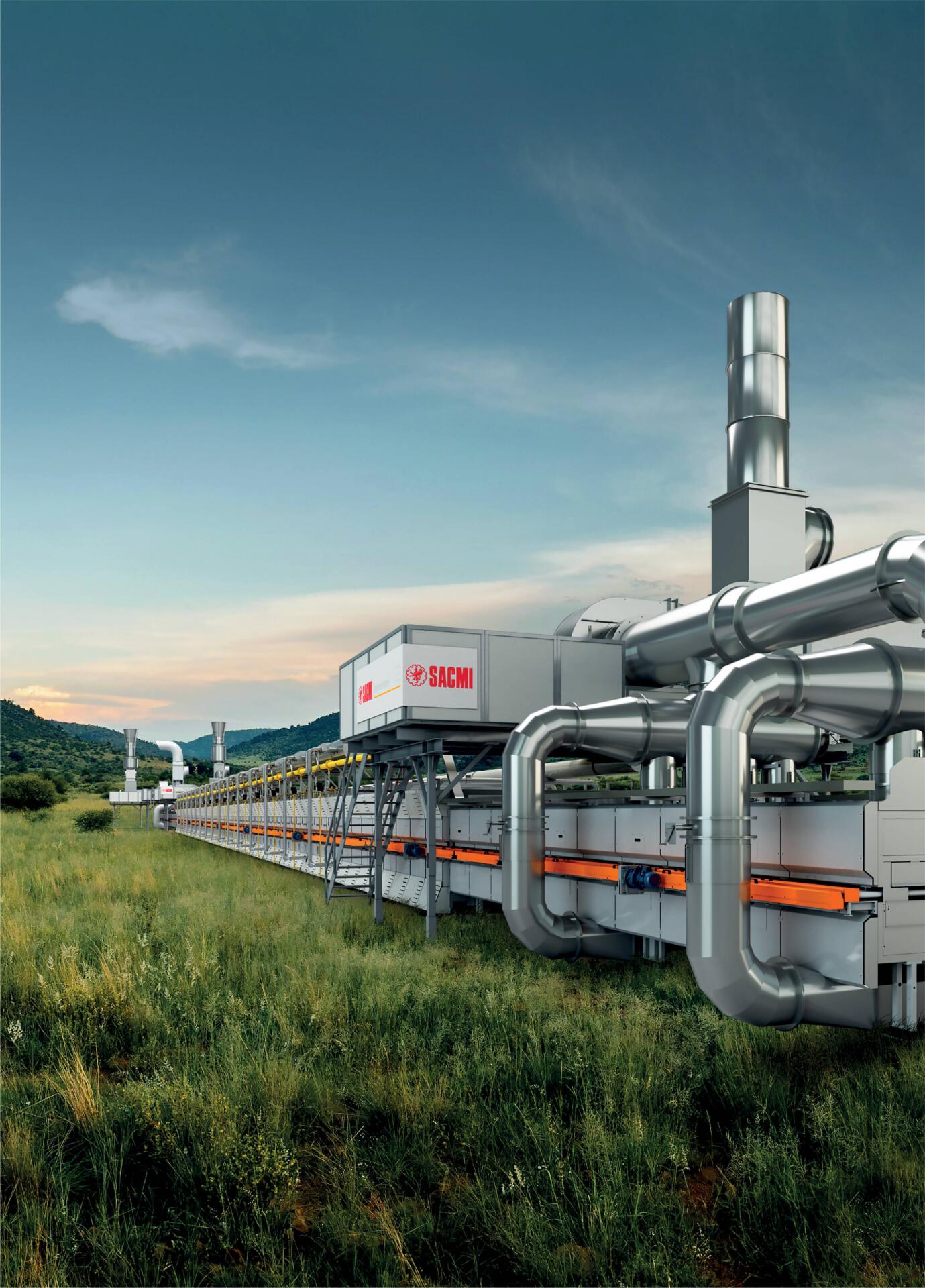
In the world of ceramics, the name of SACMI is known as the world leader in the supply of advanced technologies for Ceramics and Advanced Materials through continuous development in innovation. The company’s strong positioning on the world market, and its relentless thrive for ensuring high quality standards and customer service is praiseworthy.
The Ceramic Industry is focusing on bringing innovative solutions and effective alternatives of traditional machineries through research. The company is focused on working for development of alternative fuels, digitisation and heat recovery aimed at zeroing or reducing consumption in other stages of the process. These are the three pillars of the modern approach to ceramic kiln design, which SACMI recently presented to the market with the first prototype of a 100 per cent hydrogen-fired kiln. The presentation was made during the ‘open week’ organised by SACMI, which took place at the same time as the CERSAIE trade fair. Over 400 international customers of 90 delegations from 35 countries visited the fair.
“Making ceramic manufacturing more sustainable is the primary challenge that SACMI has been pursuing for years, implementing optimisations and innovations in all areas of the plant, from forming to firing,” explained SACMI President Paolo Mongardi. Firstly, the kiln accounts for a good 37 per cent of total factory emissions, 46 per cent if one considers all thermal processes (kiln and drier). “With the FMH Maestro, we developed the world’s first industrial kiln fired using up to 50 per cent hydrogen. Today we are taking a further step towards what will be a potentially zero-emission kiln.” The prototype is ready and will be tested to make actual products in the coming months. Meanwhile, the market is moving towards new machines with the full digital management of all parameters in order to optimise quality and consumption.
The project The prototype kiln implemented by SACMI is capable of working with variable mixtures of methane and hydrogen – in any percentage – and up to 100 per cent pure hydrogen. The kiln will be ‘switched on’ over the next few weeks, to test its effect on actual products and to take on significant technological challenges, such as the fact that hydrogen has a different calorific value compared to methane and the corrections necessary for managing the firing curves and material feed. From this point of view, the digital control of parameters (e.g. oxygen content at every point in the process) is the prerequisite of this development and has already been implemented in the ‘Maestro’ range of kilns, starting from the FMD model, introduced by SACMI in 2022.
The fuel The pure hydrogen production and storage station has already been inaugurated at the SACMI Forni and Filters site in Salvaterra di Casalgrande. The facility, one of the first of its kind in Italy, consists of an electrolyser where hydrogen is produced at a rate of 20 Nm‑ per hour. It is then compressed to increase the outlet pressure from 8/12 bar to approximately 200 bar. This is essential in order to make storage easier, since one of the ‘defects’ of hydrogen is that it is very voluminous (much more so than methane/LPG and up to seven times more voluminous for the same calorific value). The third and last station involves its storage in cylinders, which for the prototype that will be tested in the Lab, “is equivalent to an operating autonomy of 2.5 days” – underlines Daniele Baldini, product manager at Kilns and Driers BU Tiles, SACMI – “sufficient for carrying out full testing on the products”.
The advantages Currently, SACMI’s best-selling kiln globally is the modulated air-gas FMA model, which allows air and fuel mixtures to be optimised at every stage, optimising consumption and with great advantages in terms of product quality (especially for complex products, such as slabs), repeatability and consistency of the process. More and more customers are moving towards the latest FMD models (with digital firing parameter and recipe management) and FMH models (already designed for use with methane-hydrogen mixtures of up to 50 per cent). What are the real advantages of ‘full hydrogen’? You just have to consider that by adding 50 per cent clean hydrogen to the mixture, the total saving on CO2 emissions is as much as 23 per cent.
This would increase to 55 per cent (more than double) if the mixture were 80 per cent H2 + 20 per cent methane. “What remains constant is the amount of energy required for the process,” notes Baldini, adding, “while to obtain the same amount of energy, a larger volume of hydrogen is required as its calorific value is lower than that of methane (2560 kcal/m3 compared to 8600 kcal); Hence more than proportional savings in emissions to the increase in the amount of hydrogen in the mixture”. This is why it makes sense to increase the hydrogen in the mixture and to get ready for the evolution of the infrastructure, which in all probability will lead to hydrogen-methane ‘blends’ being supplied in increasing but variable amounts.
“From this point of view, the way forward already appears to have been decided,” says Claudio Ricci, Tiles R&D Coordinator, BU Tiles, SACMI. “So technology suppliers around the world are getting ready for this development, without forgetting the two conditions which make this scenario viable and truly beneficial to the environment.” First, hydrogen has to be obtained from renewable sources (or rather the electricity needed for the electrolysis process has to be). Secondly, in order for it to be actually applied on an industrial level, the problem of storage has to be overcome (the laboratory prototype is one thing; in a ‘real’ kiln the system would have to be powered directly from the supply network). The 100 per cent H2 kiln is the main but not the only development at SACMI. “By 2024 we will also present a new prototype for an all-electric kiln, exploring all the opportunities in this area as well, with the aim of being ready for the evolution of the infrastructure and the regulatory context in which our customers will have to operate,” Claudio Ricci added.
Heat recovery With SACMI, the objective of improving the energy balance of the factory by 20% is already within reach, even without considering the use of alternatives to gas. How? One of the opportunities is the ‘zero fuel’ drier, a newly developed machine, which thanks to heat recovered from the kiln, is designed to operate without fuel. Other solutions allow heat recovery systems to be used to provide energy for conventional driers and spray driers and/or to be integrated with co-generation and tri-generation solutions. The significant contribution that these systems can make in improving the energy balance of the factory has led to several projects being implemented by SACMI in the district, where high energy costs and some of the most stringent environmental regulations in the world make attention to ‘thermal waste’ management a strategic factor in terms of competitiveness.
A BCMEA Report